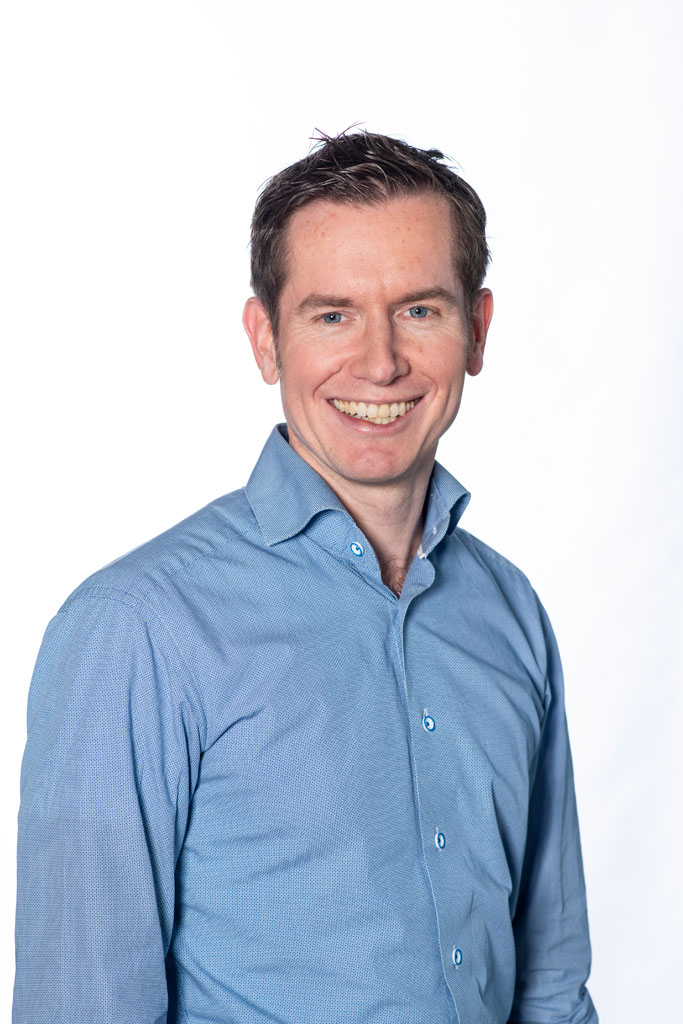
Marco Jaspers, PhD, MSc
Director Program Management & Business Development
Joined BioConnection in 2014
Marco is a director at BioConnection responsible for both the Business Development of Clinical Drug Product Manufacturing. as well as for Program Management to ensure that our client projects run smoothly.
Before joining BioConnection, Marco worked for TNO, a Dutch Commercial Research Organization, where he was a Project Manager for complex multidisciplinary and strategic Life Sciences projects, e.g. the Preclinical development of Antibiotics and DNA chip Microbial Flora Analysis. In his last years at TNO, he was also Program Manager, which means he was responsible for large projects within TNO’s Food & Health Business Line. Before TNO, Marco worked as Management Consultant at the Quality Management group of Cap Gemini Ernst & Young. Here, he analyzed the primary processes of companies and identified ways to improve these in cooperation with client teams.
Marco graduated cum laude at Wageningen University (MSc, Molecular Sciences), and achieved his PhD in Molecular Microbiology at the Swiss Federal Institute of Technology, Zurich for which he was awarded the Otto Jaag Prize. During his career, he followed various specialist and (project) management courses to advance his managerial skills (i.e. IPMA-C, Prince 2, NIMA).
BioConnection is a service provider for the (bio)pharmaceutical market covering all aspects in the life cycle of a successful Drug Product from (clinical) development to commercial manufacturing. Our Facility has an excellent manufacturing and regulatory track record (including EMA and US FDA).Our capabilities are: fill & finish (in vials, syringes) on medium (50L) and small scale, lyophilization, analytical development & validation, stability studies, and label & pack. In addition we also provide the necessary QP release services.
“We are currently looking for partners for starting up ATM manufacturing together with BioConnection. Our core expertise is maintaining cleanrooms and GMP Quality systems, and we have space in our facility to build customized cleanrooms suiting the ATM processes for our partners.”
“Our modus operandi is to work in multidisciplinary teams composed of our customers and our Manufacturing, QA and QC Specialists. Close cooperation in teams and strong project management skills are key success factors. This way, we can overcome the challenges we are often facing in our projects, ensuring timely delivery of Clinical Trial Material or commercial Drug Product in compliance with regulatory standards and our customers’ needs. Other key success factors are of course our state-of-the-art manufacturing facilities and our experienced expert teams”, Marco says.
According to Marco, this type of work requires strong adaptive skills to effectively deal with sudden changes within a project. “I am happy that our customers recognize the value that Bioconnection brings to them through our flexibility. Of course, our flexibility already starts in the early phase when Business Developers listen carefully to our customers’ needs and translating them into strong project proposals. For these proposals, technical and regulatory aspects, project budget and timelines are taken into account. We are driven to design a customized solution for each customer.”
“I am proud of being part of the BioConnection team, realizing we can make a difference for our customers by fulfilling their exact needs in (bio)pharmaceutical drug development and manufacturing and doing so in a fast, cooperative and reliable way.”